Boom Supersonic rolt XB-1-vliegtuig uit met vlucht hardware componenten 3D-geprint door VELO3D
XB-1 zal vliegen met 21 Titanium 3D-geprinte onderdelen, voornamelijk voor kritieke motoroperaties in een omgeving met extreem hoge temperaturen
CAMPBELL, Californië – (BUSINESS WIRE) – VELO3D, een innovator in digitale productie, heeft vandaag aangekondigd dat het XB-1-vliegtuig van Boom Supersonic 21 hardware componenten voor de vlucht bevat die zijn vervaardigd door VELO3D’s Sapphire 3D-metaalprinter. De XB-1, vandaag onthuld in de hangar van Boom in Centennial, Colorado, markeert een keerpunt in de commerciële levensvatbaarheid van supersonisch reizen en toont de kracht van additive manufacturing (AM), of 3D-printen, om innovatie mogelijk te maken en tegelijkertijd de productontwikkeling te versnellen.
Dit persbericht bevat multimedia. Bekijk de volledige release hier: https://www.businesswire.com/news/home/20201007005111/en/
Boom Supersonic Rolls Out XB-1 Aircraft with Flight Hardware Components 3D Printed by VELO3D
XB-1 will fly with 21 Titanium 3D-printed parts, primarily for critical engine operations in an extremely high-temperature environment
CAMPBELL, Calif.–(BUSINESS WIRE)– VELO3D, an innovator in digital manufacturing, today announced that Boom Supersonic’s XB-1 aircraft includes 21 flight hardware components that were manufactured by VELO3D’s Sapphire 3D metal printer. Unveiled today at Boom’s hangar in Centennial, Colorado, XB-1 marks a turning point in commercial viability for supersonic travel and demonstrates the power of additive manufacturing (AM), or 3D printing, to enable innovation while accelerating product development.
This press release features multimedia. View the full release here: https://www.businesswire.com/news/home/20201007005111/en/
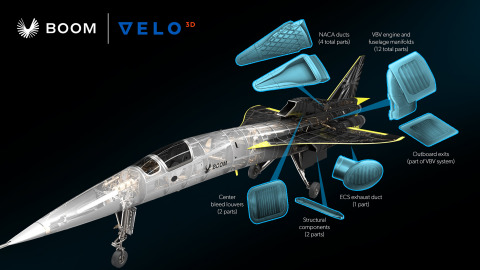
XB-1 will fly with Titanium 3D-printed components, most of which perform critical engine operations. All parts are manufactured on VELO3D’s Sapphire system. Image credit: Boom Supersonic and VELO3D
“Aviation hardware is especially difficult to manufacture with 3D metal printing, due to challenging aerodynamic designs that must be balanced with superior durability and high temperature requirements,” said Benny Buller, CEO and Founder of VELO3D. “VELO3D’s technology allows the production of lightweight, complex designs for mission-critical applications in the toughest operating conditions. Our partnership with Boom is truly an advancement for the metal AM industry, and XB-1 supersonic aircraft is a game-changer for the aviation industry.”
Boom Supersonic and VELO3D announced a partnership in 2019 to manufacture complex flight hardware to build XB-1, and ran a series of qualification trials on VELO3D’s Sapphire system. The printed Titanium parts are used for engine hardware, the environmental control system, and structural components. Characteristics of the geometric designs include tall, thin walls with high aspect ratios, which are inherently difficult to manufacture with either traditional processes such as welding and casting, or even most existing 3D-printing technologies. VELO3D’s unique SupportFree printing process enables unprecedented design freedom and quality control, eliminating manufacturing constraints to innovation in aircraft design. Read more about the collaboration with Boom Supersonic here.
“We strongly believe that supersonic is the future of flight and we’re appreciative of VELO3D in helping us to realize this goal with XB-1,” states Mike Jagemann, Head of XB-1 Production at Boom Supersonic.
XB-1 is the world’s first independently developed supersonic jet. It will be used to demonstrate critical technologies for Overture, Boom’s future commercial airliner, such as advanced carbon-fiber composite construction, computer-optimized high-efficiency aerodynamics, and an efficient supersonic propulsion system. XB-1 is the end-product of years of development effort, including multiple wind tunnel trials, dozens of structural tests, hundreds of simulation iterations, and tens of thousands of work hours.
View source version on businesswire.com: https://www.businesswire.com/news/home/20201007005111/en/
Contacts
Joyce Yeung